Project Description
During the summer of 2009, I performed research at Southern Methodist University through the National Science Foundation’s Research Experiences for Undergraduates (REU) Program. Working in Dr. Radovan Kovacevic’s Research Center for Advanced Manufacturing, I helped develop components for an electron beam welding/plasma window system. Electron beam welding uses a stream of high velocity electrons to fuse two pieces of metal, but typically requires the entire system to be sealed in a vacuum chamber in order to produce the beam. For large work pieces, evacuating an air chamber is a time consuming and costly process. The addition of a plasma window allows he electron beam to be generated in a much smaller vacuum chamber. plasma window allows the electron beam to penetrate, without allowing air to enter. Moving the electron beam/plasma window along the workpiece will allow large pieces to be welded without needing a large vacuum chamber.
I worked on various projects to help build the first prototype of this system. Shown above, I designed a mechanical test stand for the system and performed FEA analysis to ensure the stand could support the requisite 2000 lb of lead needed for a protective shield. I also developed a manifold for the electron beam cooling system, allowing precise measurement and control of the flow rate through various portions of the system. Additionally, I designed custom aluminium components (e.g. brackets, pressure covers) needed to integrate off-the-shelf components. I fabricated these parts using in-house equipment including a 5-axis CNC mill and waterjet cutting machine. The final poster presentation for this project is pictured below.
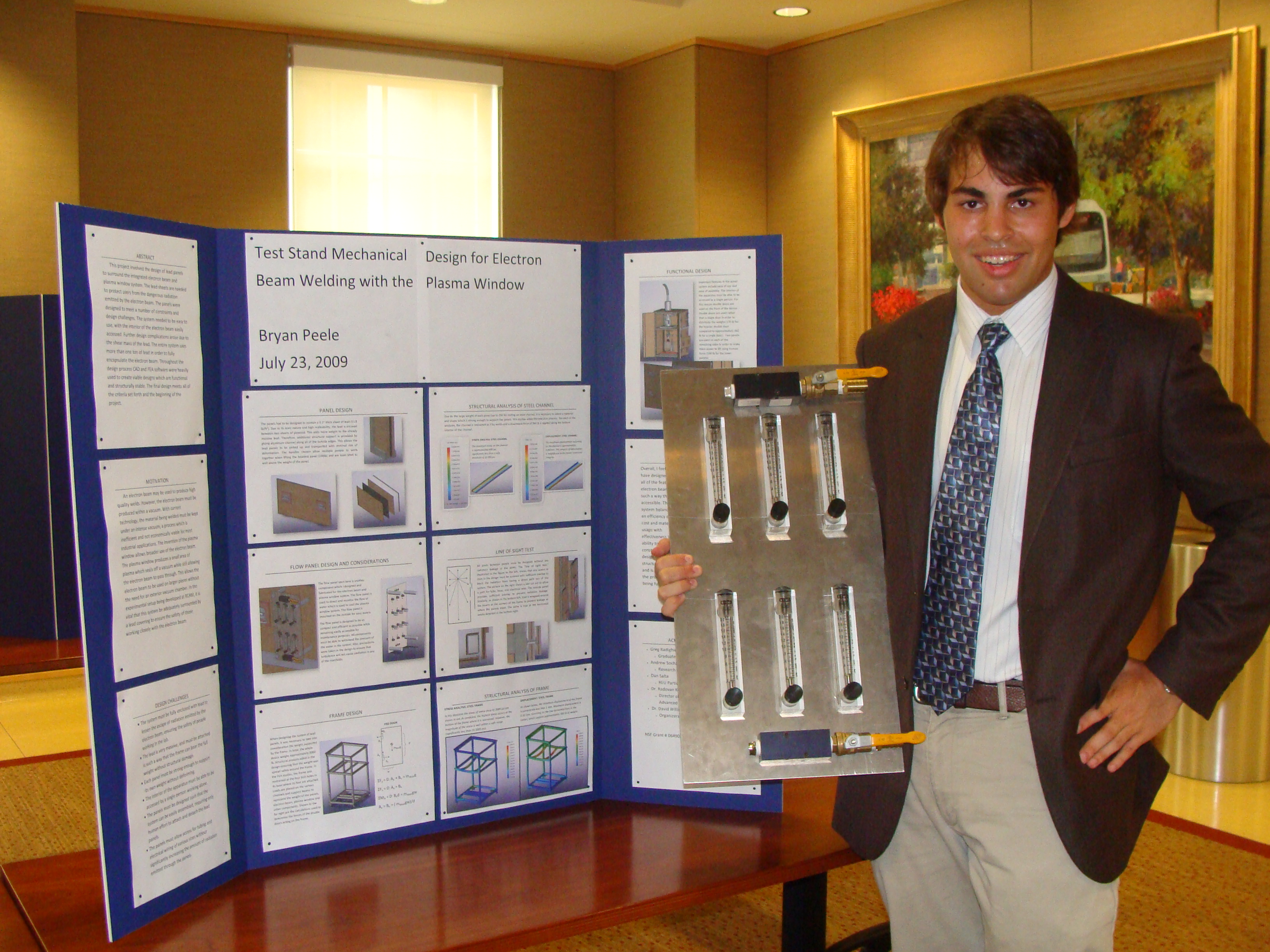