Project Description
During the summer of 2011, I worked as a researcher in Dr. Seelecke’s Multifunctional Materials Systems Lab at the Universität des Saarlandes in Saarbrücken, Germany. My work focused on the use of Shape Memory Alloy (SMA) wires to mimic the function of biological muscles. First, a kinematic model of the bat motion is developed in order to determine the desired joint movements needed for flapping flight. Then, a physical prototype is build that uses the contraction of SMA wires to control these movements.
- Publication: Design and Fabrication of an SMA Actuated Bat
- Poster Presentation: BATMAV-poster.pdf
Kinematic Modeling
In order to provide a realistic flapping motion, a simplified model of the bat wing is developed and tuned to match data collected from actual bats. A kinematic model shown to right, labels key components of the bat anatomy. For this model, I have included three degrees of freedom (DOF). The should, elbow and wrist joint are each allowed to rotate along a fixes axis. A sinusoidal function is applied to each joint, with amplitude, phase and frequency chosen individually to approximate the motion of a bat wing during horizontal flight.
The figure shown below shows the resulting trajectories. Black lines represent the wrist and wingtip trajectories from the kinematic model. The red trajectories represent data collected from actual bats.

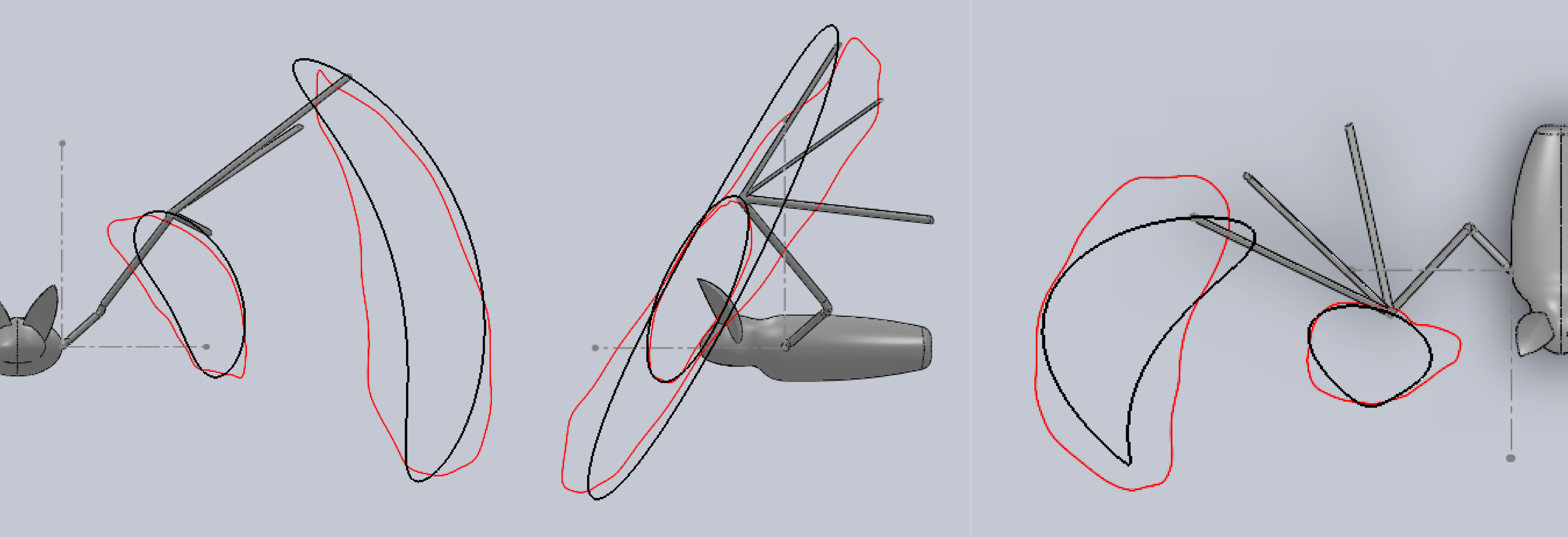
Physical Prototyping

Physical prototypes from this project are currently on exhibit at the Nature Research Center at the NC Museum of Natural Sciences. Shown to the left is a static model that is taken from a series of models developed to show the full cycle of motion. This model was fabricated using multimaterial 3D printing capable of printing the rigid bones and flexible wing simultaneously.
The video on the bottom left shows the CAD model for an active bat with holes built into skeleton to route the SMA wire appropriately. The video on the bottom right shows the completed prototype on display as a museum exhibit. When a button is pressed at the exhibit, the bat wing moves though a full flapping cycle.